Project
Bottling Line Design
Juice and Dressing Manufacturer
The Problem
Agilitech collaborated with a local food manufacturer to provide automation and design services to employ enhancements to their current operations in juice and dressing lines. Key focus areas included the need to improve line efficiencies and optimize or reduce labor.
Our Solution
The Agilitech team worked with the client to complete multiple design iterations and provided capex budgeting for various design concepts allowing the customer to select the optimal solution to meet their budget and schedule.
Our team provided process flow diagrams, along with materials flow analysis, to properly size the automated transfer from the bottle filling lines into the HPP (High Pressure Processing) pasteurizer, and out to labeling and casepacking. The project included upgrading several of the SKUs with new caps and labels, researching new OEM vendor equipment, adding leak detection equipment, and more automated palletizing.
The upstream equipment flow was redesigned to reduce the hand pack operations required before the HPP process. After the HPP, the flow was redesigned to allow for new labels, leak detection, and more automated casepacking and palletizing.
The Results
Through optimized process design, equipment upgrades and tailored automation Agilitech was able to address the client’s specific pain points, increasing line efficiencies and reducing unnecessary manual labor. For example, automated palletizing reduced labor and OSHA incidents, while increasing throughput.
Agilitech worked with the client to develop several levels of automation, and generated capex budgets to support each variation. This allowed the client to select the best fit for their current and future operational requirements.
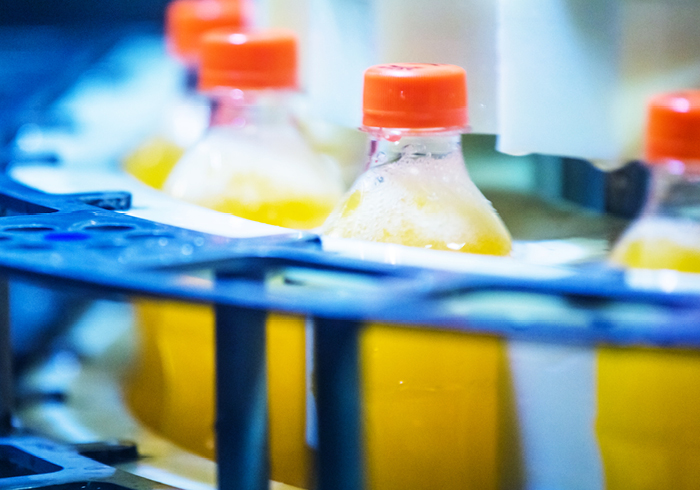
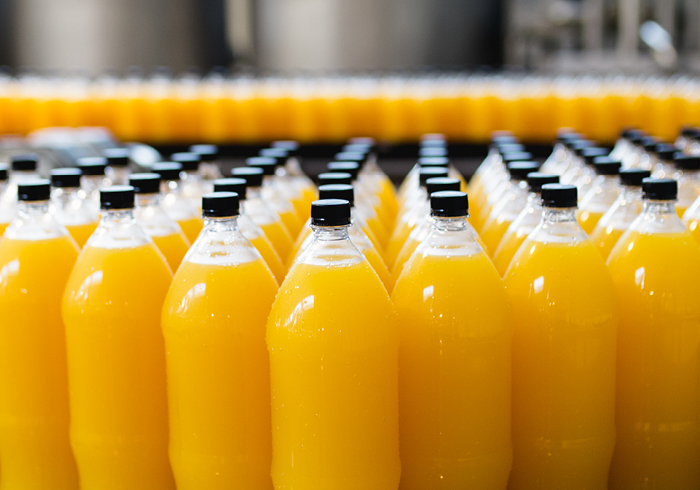