Project
Aseptic Packaging Line
Food Maufacturer
The Problem
A local food company with whom Agilitech had a long-term business relationship was awarded a new contract that required the following: the installation of a second cup line; upgrades to address the room conditions required for the new cup line; and increased capacity for the exsiting cup line, kitchen batching, and recipe implementation.
Our Solution
The Agilitech Food and Beverage team worked closely with the client to generate a complete design that included process flow and equipment selection, meeting sanitation requirements, and maintaining product quality. Our process design team developed the process flow for recipe and batching, selected instruments and equipment, generated HMI screens, and delivered product to the filling line.
The packaging design included the aseptic cup filling, lot and date coding, as well as feed conveyors to transfer the cups into and out of a spiral cooler, and finally into a wraparound sleever and casepacking system.
Our automation team programmed the recipe batches, integrated the CIP process, and built several control panels to tie the entire line into a complete automated system. We then managed the OEM vendors as well as provided PM and CM support throughout the duration of the project.
The Results
Agilitech upgraded their equipment and systems, and optimized their complete process for quality, efficiency, and safety. Agilitech continued to work with the client to upgrade their packaging room to a more food-safe environment, improve their CIP system capacity, and increase their pack line efficiency.
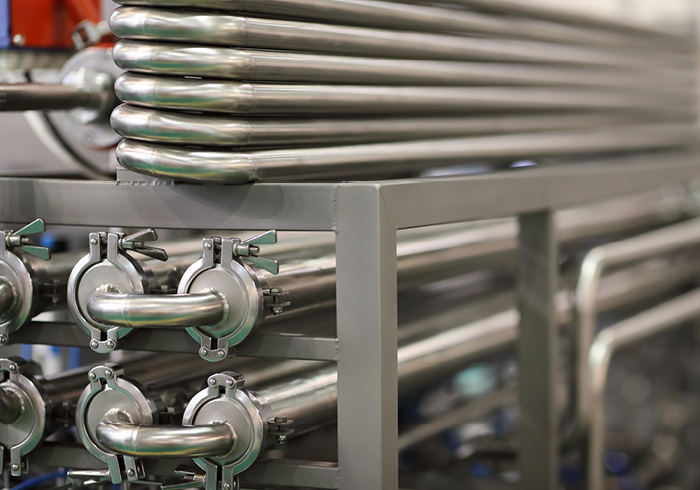
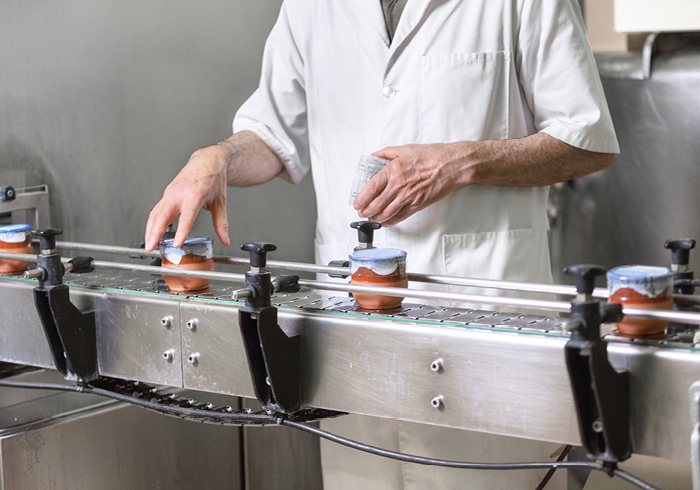